Characterising the prefabrication workforce
An analysis of the current supply of and demand for the prefabrication workforce
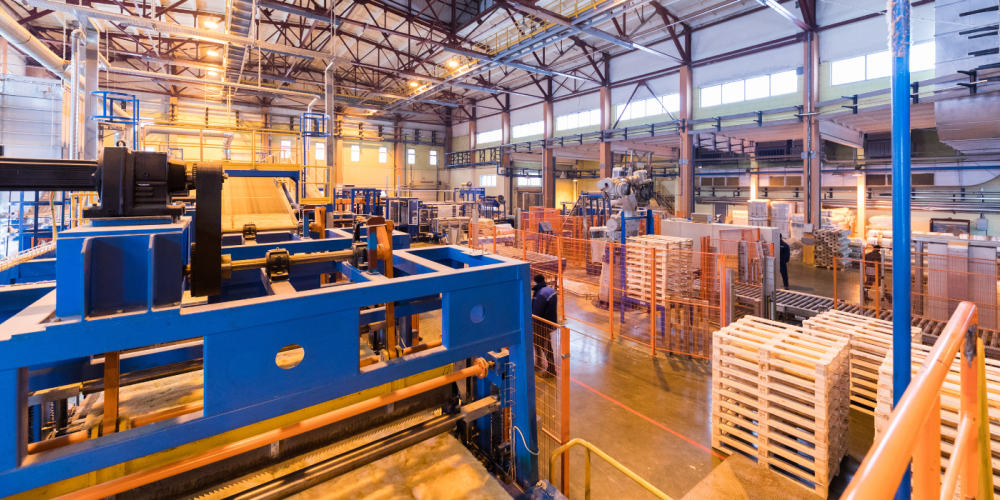
Unlocking the potential of offsite manufacturing
Portfolio Manager: Mani Saini
Did you know that we could be building quicker, higher quality, more sustainable homes? Offsite Manufacturing (OSM) is here to reimagine how we build and revolutionize the industry.
From 2014 to 2021, construction projects using at least one prefabricated element jumped from 3% to 9%. Going forward, it’s expected to skyrocket even more. The government has responded to the Residential Building Supplies market study by the Commerce Commission by pledging to boost their use of OSM by at least 10% every year.
Using the philosophy of “If you can’t measure it, you can’t improve it”, ConCOVE set out to understand the size and composition of the current and future prefabrication workforce. We partnered with Scarlatti to develop an interactive dashboard integrated on Waihanga Ara Rau’s Workforce Information Platform (click here) to house this information.
A Closer Look at the Workforce:
The project estimates there are 2,325 Full Time Equivalent (FTEs) (Q2 2023) making up the prefabrication workforce across Aotearoa New Zealand, while the demand for the same time period is estimated to be 3,999 FTEs. The shortfall in FTEs isn’t just because there aren’t enough people, but also because of how the numbers are crunched.
The prefabrication workforce is currently composed of the same occupations you would find in a traditional on-site build. We think this is because majority of the prefabrication industry here is labour intensive.
A presenter at the recent Offsite NZ Colab 23 conference summarised this, “we are simply building bespoke houses in big garages” – we build the same way as we traditionally would, except we do it indoors and offsite. However, we expect that as new technologies within the OSM sector are adopted across the sector, the composition of this workforce would change, with more technology intensive roles becoming relevant.
Here’s where you come in – if you’re part of a prefabrication business in New Zealand, you can help make this data even better. Head over to the dashboard and fill out the feedback form. This will help us understand the future skills required by the industry and ensure that the right vocational education is in place for this demand.
Insights into the future of the prefabrication workforce
We wanted to model the future of the prefabrication workforce against pipeline of work data. While the future OSM market share is expected to increase, it is difficult to gauge by how much.
We also expect that as the sector matures, it will adopt more technology-heavy means of production, reducing the number of overall staff that may be required for the same production rate. However, once again, it is difficult to gauge what percentage of the OSM market will be technology-intensive rather than the labour-intensive market it is today.
To this end, the interactive dashboard allows the user to change the OSM market share from the current 9%, to an estimated 20% or 30%. Similarly, it also allows the user to change the technology adoption rate from 0% to 10%, 20% and 30%.
These potential scenarios give us incredible insights into the workforce size and composition, for example: With high technology adoption, the total number of people required in the prefabrication workforce decreases, even though the OSM market share increases, and even with the overall size of the construction workforce increasing 3% year on year.
This insight speaks volumes about the productivity gains from a combination of the use of prefabrication and the adoption of technology within prefabrication.
Recommendations and further research
The modeling work has provided a much-needed starting point to better understand the prefabrication workforce and its future. But the modeling work isn’t just numbers and graphs – it’s a call to action. Here’s what needs to happen:
Embrace technology:
Adoption of technology can be used to offset the increase in demand for the prefabrication workforce if the industry were to struggle to attract the required people.
Education is key:
With an increase in technology adoption in the OSM workforce, the ability to embrace, interact and be proficient with digital technology will be a key skill required of the workforce. It is strongly recommended that generic digital skills are embedded into the vocational education going forward.
Keep the conversation going:
Further research into the implications of prefabrication businesses widely adopting technology is required, along with further research into the future skills that would be required as a result of the evolution of the OSM industry. There is also a need to coordinate with key players in the sector including Construction Sector Accord, Waihanga Ara Rau and Hanga-Aro-Rau to ensure alignment and delivery of next steps.
Click here to view the interactive dashboard (and provide feedback)
For details on the included scope, methodology, relevant references, and more information, please review the complete report here.